The complexity of solar projects doesn’t need to slow you down.
A typical survey using manual methods can easily take 30-60+ minutes, and the majority of Designers say this leads to revisions 25-50% of the time. Surveying with a drone and mobile app is not just safer because it minimizes roof time, but it takes 50-90% less time. Digital checklists are a key tool for simplifying and standardizing different stages of a solar project’s life.
There are a wide range of benefits to using digital checklists. First, Surveyors work on a standardized, digitized process that ensures all data is centralized in the cloud and organized by project. This maximizes data collection efficiency, ensuring no data point is missed. Further, having all checklists in one place lets you centralize the entire project on one platform, keeping contractors and their personnel organized. Finally, checklists can be automatically shared with property owners, lenders, designers, and other partners for easier collaboration.
Here are five of the most common checklists we see and a few niche cases that require nuanced approaches to fieldwork.
1. Surveying checklist
A surveying checklist confirms all the information you need to inform the final design that a customer will sign off on—and procurement and installation planning will work with.
Key information to collect:
- Property data such as owner info and any known pre-conditions provided by the site owner.
- Pre-site review, including notes from satellite imagery.
- Information provided by the customer, including blueprints, if available.
- Roof measurements and condition, including any damage.
- Attic structural context, including rafter details and any damage.
- Electrical information, including panel size, age, damage, potential interconnection method and location, and potential locations for future electrical equipment to be installed.
Additional details about the site, including obstructions, outbuildings, trees, and any household pets.
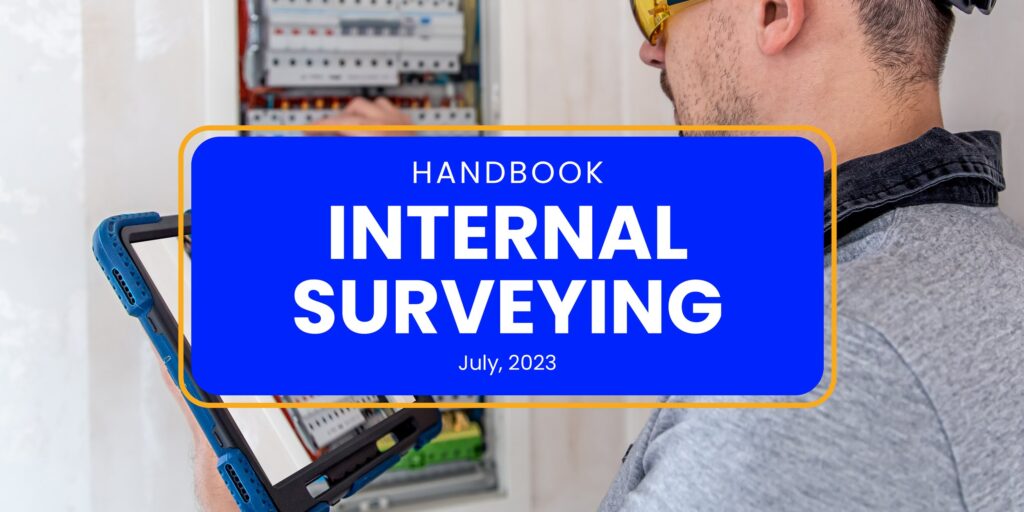
2. Installation checklist
This checklist ensures that the Installation team can do their jobs properly and without delays.
Key information to collect:
- Project and team info, including who is staffed in what capacity.
- Pre-installation assessment, including racking placement and pre-existing damage waivers.
- Safety review, including anchoring, harnessing, and work-zone outline.
- Array plan including materials, flashing, and panel mount locations.
- Electrical plan including grounding, conduit runs, and sticker maps with inverter serial numbers.
- Post-installation photos to confirm the job is done and to compare against any pre-existing damage.
Site cleanup to ensure no materials are left behind and any mess is dealt with.
3. Commissioning checklist
This checklist contains the final steps you need before a utility can turn the solar system on.
Key information to collect:
- Electrical check, in particular against any AHJ rules for the area.
- Structural check, including panel mounting security and ensuring the roof is sealed at any puncture points.
- Safety check, including a clean job site with all other safety documentation (e.g. necessary upgrades or maintenance) completed.
- Commissioning test, including a check on the inverters, panels, and production tracking app.
4. Maintenance checklist
This checklist is used for diagnosing any issues post-installation and commissioning. The data found here will then inform any O&M steps you may need to take.
Key information to collect:
- Initial project information including site details and pre-existing damage.
- Review installation details to familiarize yourself with the array size and location.
- Roof and panel diagnostic check, looking for signs of damage.
- Electric diagnostic check, including all materials such as inverters, conduits, and panel switches.
5. Warehousing checklist
This list contains all the essential items you’ll need on hand for solar projects. This entails all the hardware and materials that must be loaded into the trucks for install day or a maintenance run.
Key information to collect:
- Electrical materials like inverters, conduits, casings, and grounding materials.
- Array elements like panels, inverters and racking equipment.
- Safety materials like harnesses, hard hats, ladders, and tie-in ropes.
- Technological elements like routers for tracking the production of installed systems.
On top of checking you have each item, it’s helpful to have a standard number of parts each truck is expected to have before going out.
Checklists for unique use cases
While the five checklists above apply to nearly every project, there will be some unique or niche use cases that have their own needs.
Battery or EV charging projects: On top of typical project information, you’ll also need a preliminary site review for the mounting location of the battery/charger and more electrical details to plan the connection between the PV system, charger, and electrical panel.
Ground-mount PV systems: In the preliminary site review, you’ll need additional details like service riser information, meter location, and number of ground mounts. Further, you’ll need information about the ground site such as slope, materials, and foundation plans for the PV system.
Extensive or large commercial surveys: This will be similar to a regular residential or commercial site, but you’ll need more detail about the roof, including beams and rafter materials, and a more in-depth understanding of conduit runs and electrical panel capacity. You’ll also want information about on-site parking and anything else that could impact either the array itself or installation plans.
Standardize and streamline to save time and money
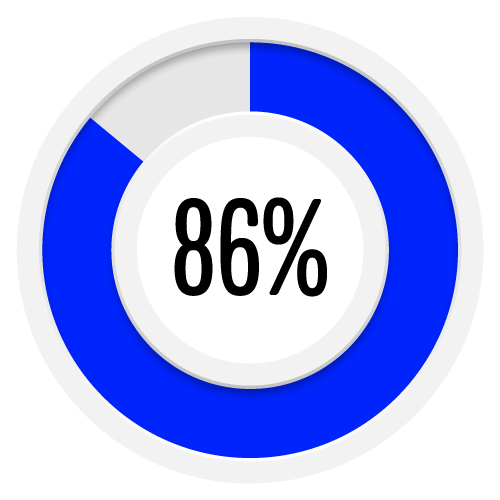
While checklists help, they cannot fix inaccurate data. The majority (86%) of Surveyors say that inaccurate data from manual measurements is a huge bottleneck and problem in solar. Similarly, more than half of Designers say manual surveys cause headaches for their work, often leading to redesigns or change orders.
This problem can be fixed with technology—and that same technology can drive even more benefits.
When you have consistent and accurate data collection, your procurement and installation teams can scale up more easily; you won’t need to double back or waste time on revisions. With the average residential revision costing $750 between labor and additional truck rolls, these savings can add up quickly. Ultimately, you deliver a higher-quality customer experience, leading to a better business.