Sometimes going on the roof is necessary. But why prolong it and put Surveyors at additional risk more than you have to?
Being up on the roof is fundamentally risky: 64% of Surveyors report accidents like dropping equipment. Going on the roof is also cited as one of the least favorite parts of the job; further, Surveyors often cut corners for the sake of safety (and who can blame them?).
Are we willing to put human life at risk because of a preconceived notion that business should be done as it always has been? Just because you’re on the roof for some work (like a structural check), you don’t have to do everything manually. Besides, harnessing in for safety might protect workers, but no homeowner wants extra holes in their roof before install day.
Instead, the goal should be minimizing time spent on the roof and only climbing up when necessary.
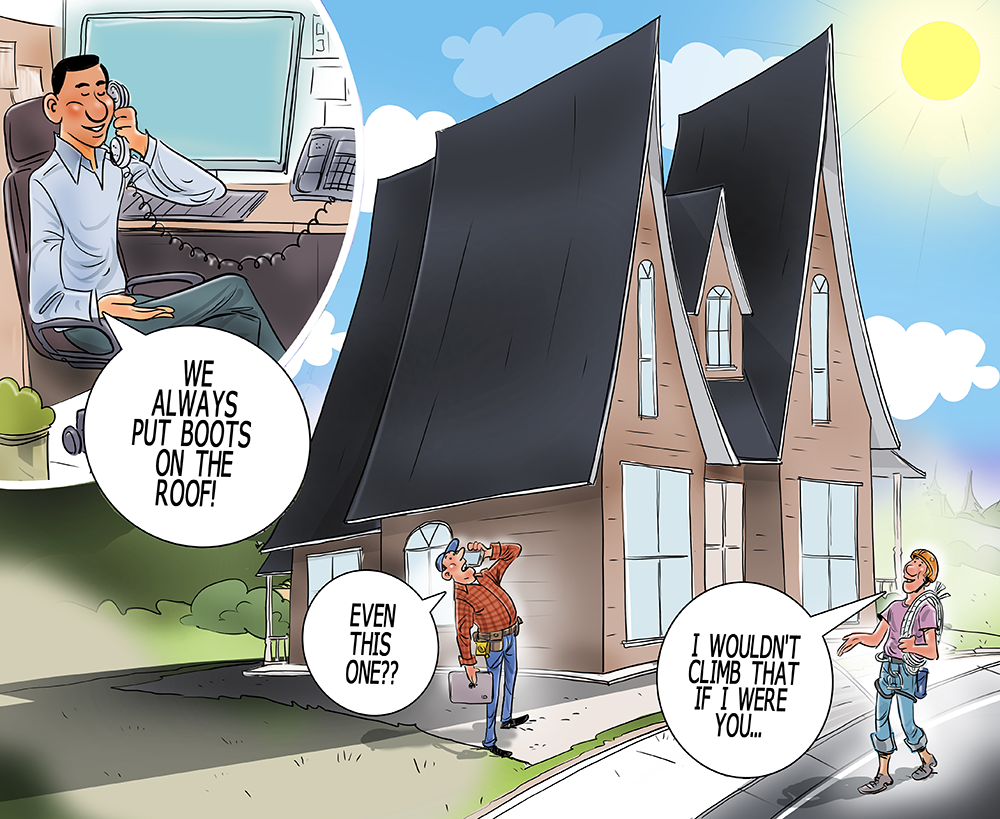
What Information is Commonly Captured in a Site Survey?
Start by asking what data you want to collect from the roof.
Usually, it’s the same data points:
- Production estimates: Measurements and shade analysis
- Array design and location: Identifying and measuring all roof planes
- Roof structural safety: Checking for soft spots or damage
Depending on your business structure, you might also want to identify upsell opportunities. For instance, a homeowner needing a new roof or using the survey as an opportunity to talk about heat pumps or electric vehicle charging.
When is Manually Collecting Data Detrimental to Project Quality?
Being on the roof is not just unsafe for humans—in many cases, it’s not the best way to collect certain data.
1. Measurements
The majority (86%) of Surveyors and Designers acknowledge incorrect manual measurements are the leading cause of survey mistakes.
Drones, on the other hand, are equally, if not more accurate to a high-quality manual survey, but without the human error risk.
Even if your Surveyors are perfectly accurate every time without fail, chances are they are only measuring a couple of roof planes or using satellite imagery with significant setbacks. If that isn’t the case, they are probably taking over 60 minutes to conduct the survey. All of these situations amount to suboptimal systems and processes, either because array designs might change or you miss out on additional panels due to unnecessary setbacks.
2. Production Estimates
If you default to aerial or satellite imagery, you risk grainy 2D models with skewed angles, the result of which is not fully accurate measurements. This could be multiple inches off of true, meaning you might lose a line of panels going from preliminary survey to final design—a huge issue if you offer production guarantees.
The same goes for shading; not doing on-site shade analysis often results in poor results, which again impacts actual production compared to estimates. What’s more is Surveyors know this already, with 81% acknowledging on-site shade data is better than remote data due to issues around skew and data recency.
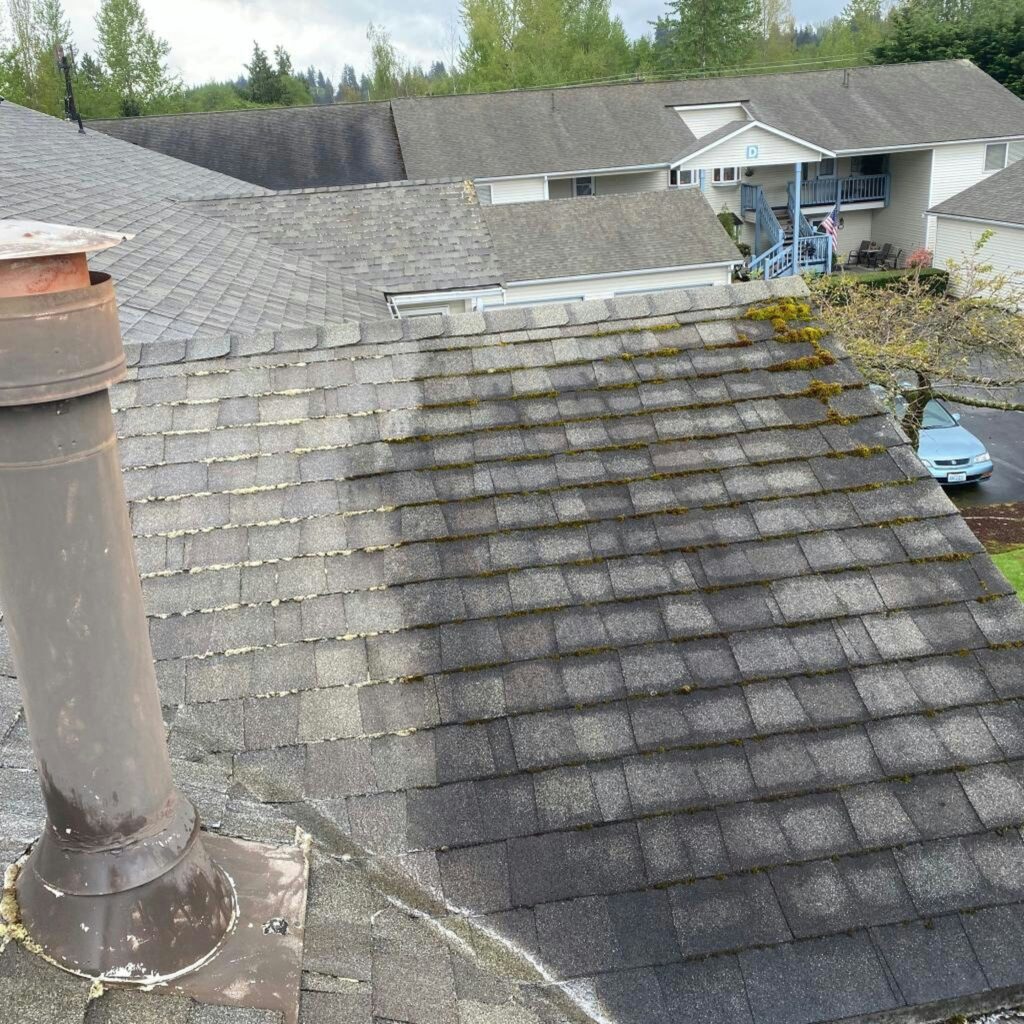
Using drones, you can easily build a whole-site 3D orthomosaic map that shows every tree and shade-causing element. This gives you more accurate production estimates you can stand behind in your pitches.
3. Roof Shingle Health
If your goal is to check for shingle layers or conduct a clay hammer test, you can climb to the roof edge, making the job safer, equally accurate, and more efficient. Similarly, if you can see rafters from inside, you don’t need to climb on the roof.
When is Going on the Roof the Only Way to Ensure Quality?
Climbing on the roof pre-installation is only truly necessary to validate roof structural health (since satellite imagery simply can’t do the job properly and drones cannot tell you everything about roof health). The only exception is a new construction, since you can work from builder blueprints.
If you are working in an older home where you can’t access the attic and see rafters, then the only way to get the job done is climbing on the roof.
What am I Giving Up by Sticking With Old Ways?
The mindset of “there’s one task that requires a roof climb, so collect everything while you’re up there” causes a lot of problems.
1. Safety: The longer someone is on the roof, the higher the risk of accidents. For example, 37% of Surveyors say they’ve refused to climb on certain roofs for safety reasons; this often results in losing revenue Contractors could have won if they used drones.
2. Speed: A comprehensive survey can easily take 30-60+ minutes, even on a simple roof. A drone, on the other hand, takes about 10 minutes and gives you more time on the ground to talk with customers or hustle to your next site.
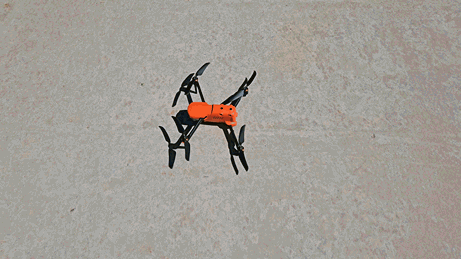
3. Accuracy: Drones are more reliable over the life of multiple projects. Even if you have a great employee, this is not sustainable as that person wants to go on vacation, may get sick or injured, or simply burns out of the physically intense job that is manual surveying. Then there’s simply daily exhaustion—there’s no way a surveyor will have the same vigor on the last job of the day compared to the first, especially in scorching heat or freezing winters.
4. Talent attraction and retention: Solar has a significant and growing talent gap—the last thing you want is people burning out from intense manual work. On the other hand, you may have trouble recruiting more experienced talent who simply doesn’t want to climb on roofs all day. Leveraging technology, you can keep your current people longer, have them do more projects, and tap into a new talent pool.
5. Sales: Surveyors can be some of your best salespeople—they are technically knowledgeable and already on-site, so leverage them and the cool factor that comes with using technology.
Only Go on the Roof When Absolutely Necessary
We’re not saying you avoid the roof entirely—it is rooftop solar, after all. Instead, we’re saying minimize roof time and focus on what you truly need to collect manually rather than a mindset of “well, we’re up there already and this is how we’ve always done it”.
In an ideal world, Surveyors are able to use technology for the least safe parts of the job, only climbing on the roof for small periods of time and for specific tasks. The result is a safer process that gets all the information you need for a successful sale and installation.