A “good,” comprehensive plan set enables a design process that yields no revisions, permitting delays, or install-day call-offs. These are all essential as the solar industry grows, yet 66% of Designers have to deal with revisions on a regular basis. Quality-focused Contractors consistently balance speed with quality, attempting to maximize their team’s resources.
Bad plan sets, on the other hand, are rife with small omissions and errors that contradict AHJs, contrast with utility regulations, and make things difficult for Procurement and Installers. These often lead to many of the revisions Designers face.
Here are the characteristics of each—and how to avoid the costly problems caused by a bad plan set.
What makes a good plan set?
A good plan set is one that Engineers can easily compile and stamp so Procurement can order what they need and Installers know exactly what’s going to fit on install day.
That requires a few elements:
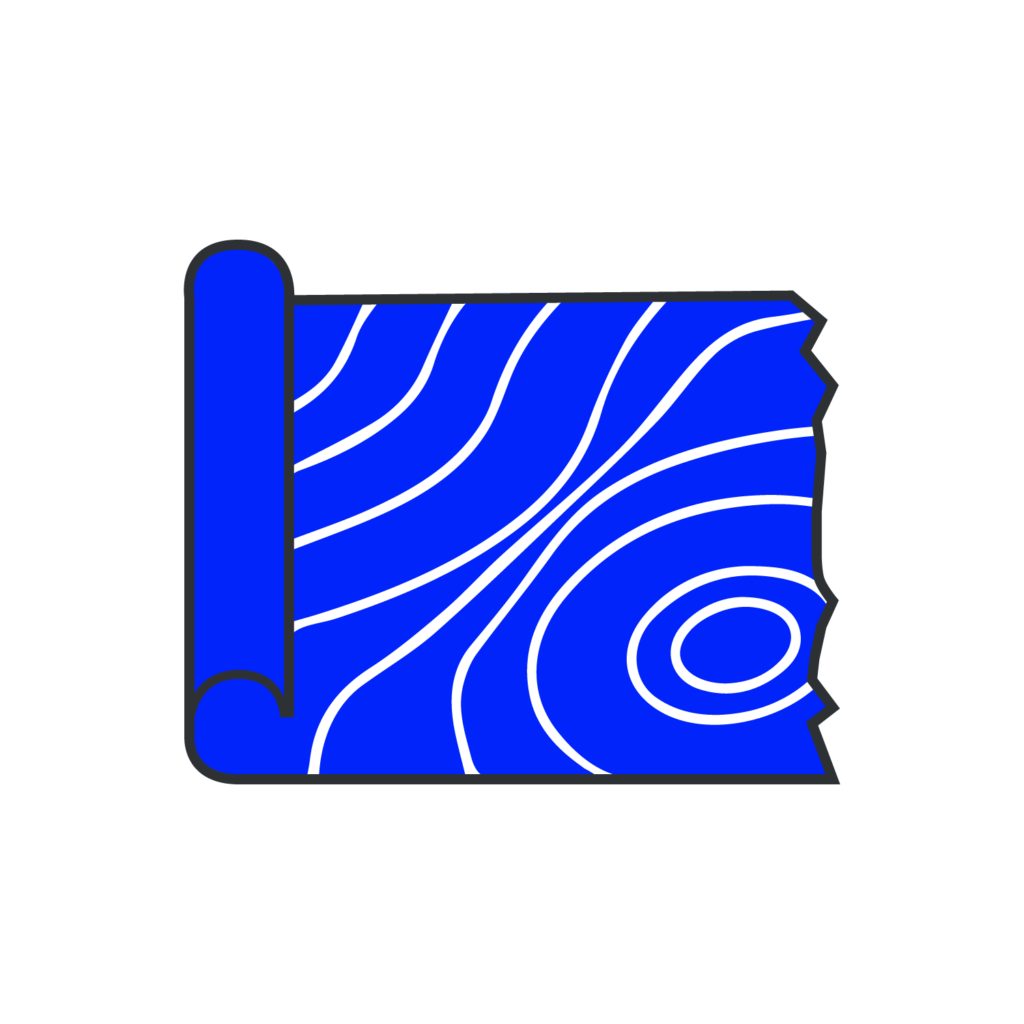
Property overview:
- General map of the site for contextual and permitting purposes
- Correct address (and any navigation information for rural or hard-to-find properties)
- An orthomosaic map to ensure accurate visual planning for the array
- Drawing property lines, including driveways, boundaries, and other details and callouts
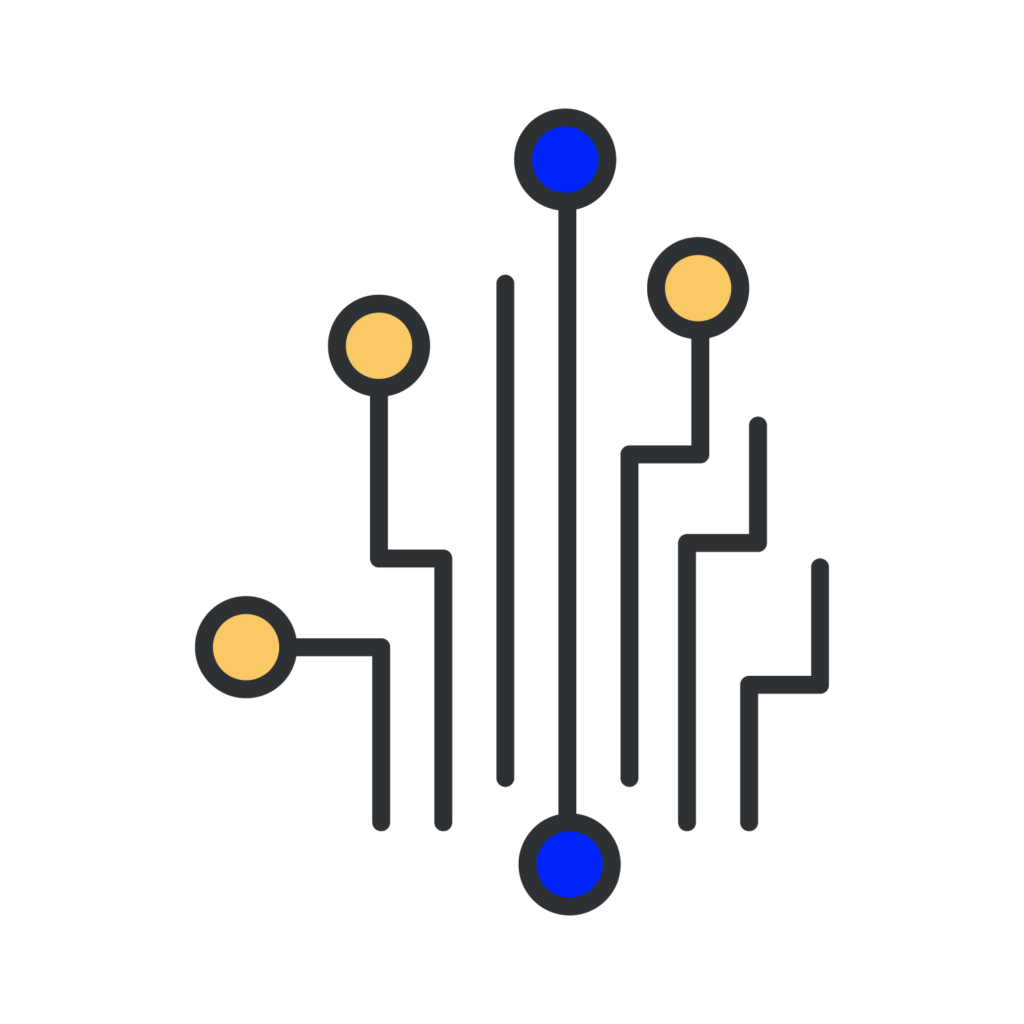
Electrical information:
- A one-line plan that shows the electrical wiring flow
- Electrical plans so your team can see how the system plugs into the main service panel (MSP)
- Indications of any electrical upgrades
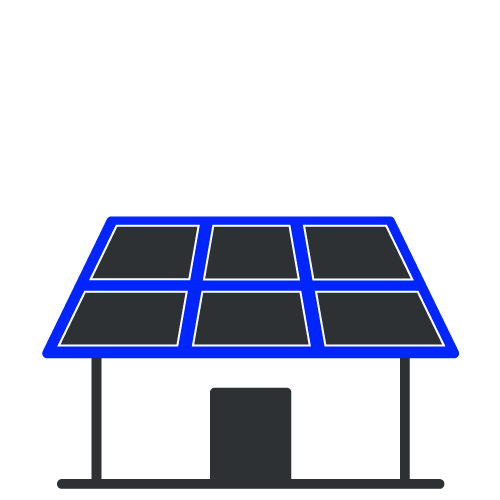
Array plan:
- Roof plans that outline panel placement
- Mounting info so your Installation team can safely attach racks and panels
- Square corners to avoid visual slanting and installation day issues
- Bill of materials so your team can order the correct supplies
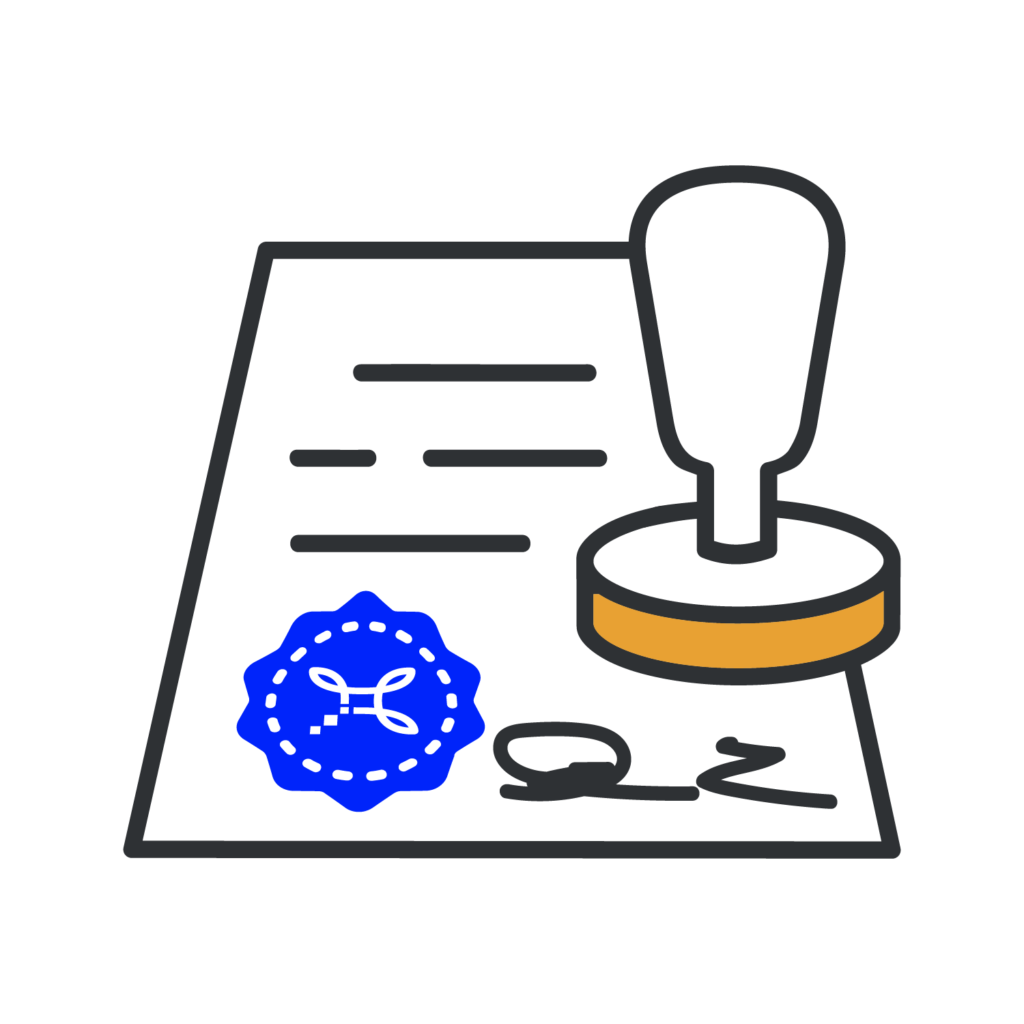
Stamps and placards:
- Spec sheets of hardware being used for permitting and installation planning
- Placard showing engineering sign-off
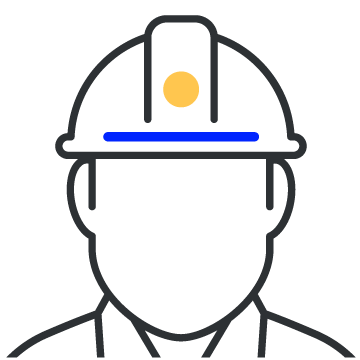
Additional needs:
- Clearly addressing any unique or niche AHJ rules (e.g. template labels or specific approaches to calculations, such as voltage drop)
- Calling out specific utility requirements (e.g. fire zone setbacks)
And, of course, do a quick grammar and spell-check on the plan set before submitting it. This is less about catching small typos and more about ensuring all technical components are labeled correctly and details are easy to understand for Procurement, Installers, AHJs, and utilities.
All of this information is best collected by (1) a drone to capture the external / roof data, and a mobile app for internal information, specifically digitizing electrical and structural data.
Where plan sets can go wrong
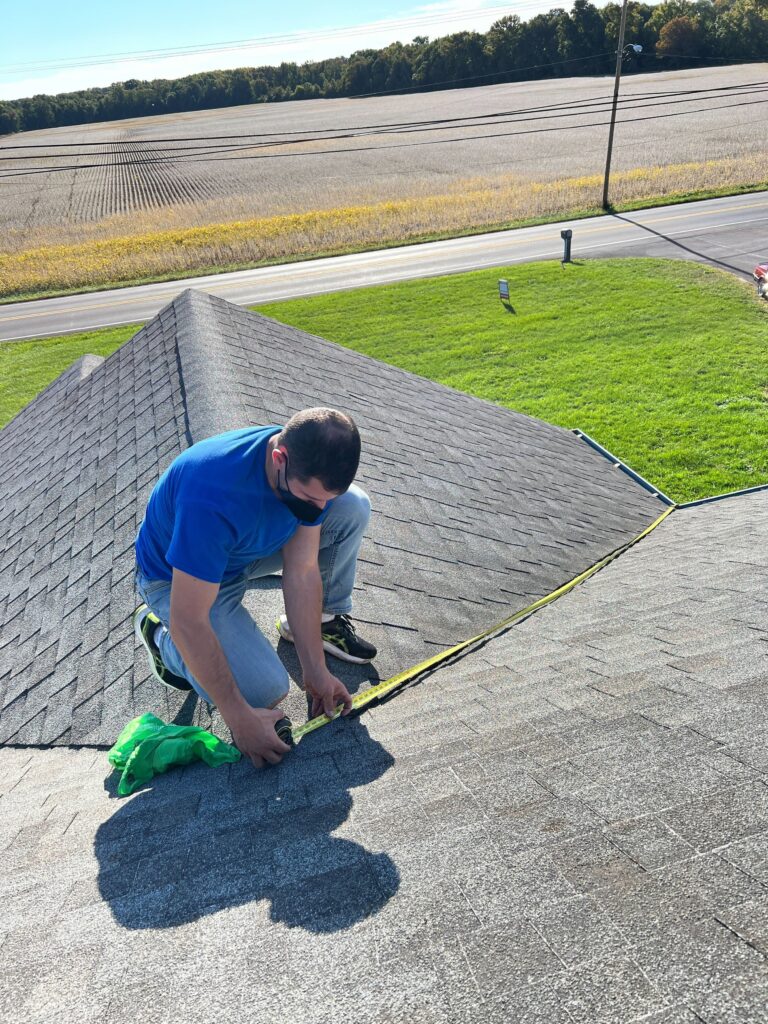
Here’s how a bad plan set happens:
Limited upfront information: As the saying goes, “garbage in means garbage out.” Designers need accurate, comprehensive on-site information, and 86% say that incorrect data from manual survey methods is the leading cause of errors, revisions, and delays. Roof climbs, tape measures and paper and pencil just don’t scale in an operationally efficient way.
Not factoring AHJ requirements into plan set templates: Sometimes requirements will change how you present information, so make sure you create new templates for each AHJ you work with.
Unclear language: If something is mislabelled or isn’t presented in the specific way that an AHJ or utility needs, it’s more likely that you’ll get a kickback or revision request.
Not updating plan set templates: Mistakes or omissions can happen, but it becomes a real problem if you don’t update templates to avoid making the same mistake twice. When you update templates, make sure you’re not inadvertently causing other problems by changing a separate piece of the plan set.
How plan sets get made
Plan sets can be produced in-house or through a third-party partner.
Working in-house provides the opportunity to be incredibly detailed or handle niche and complex projects. However, in-house design teams can be expensive to maintain, may limit the types of projects you can take on, and just take longer.
On the other hand, outsourcing delivers quick results (less than 48 hours), but it may take some extra leg work to design templates for highly specific AHJ use cases. It can also be hard to pivot quickly or develop incredibly granular outcomes for certain projects. However, even with these potential challenges, outsourcing is often far more efficient.
“Drafting in-house took much longer,” said Ethan Goddard, VP of Energy Technology at Solar Energy Services. “The turnaround time [with Scanifly Design Services] is tremendous.”
The importance of an experienced plan set team
Whether in-house or outsourced, the key to success at the start will be setting up initial templates and being keenly aware of local rules.
For an outsourced design team make sure you over-communicate system requirements up front; include all local AHJ requirements and other details to avoid downstream issues. Then be available to address any mistakes or issues as they happen, updating templates as needed to ensure a scalable and consistent process.
If you’re curious to try out a third-party partner, work with Scanifly Design Services on a new project or one you’ve already completed, to compare results and quality.