The process of taking a preliminary layout to the final system design requires on-site data.
This isn’t about preference; it’s about quality and accuracy. While some information can be collected remotely, the Engineering and Procurement requirements, such as roof structural data and electrical panel information, almost always need to be collected on-site.
Without comprehensive, on-site data, Designers are stuck wasting time and making educated guesses to get the plans “accurate enough” — words every Installer hates.
Where on-site data is essential for Designers
While some projects (e.g., new builds or homogenous suburbs) may be able to use plan sets or blueprints alone, the majority of solar array plans require information that can only be collected on-site.
1. Structural analysis can only be done on-site
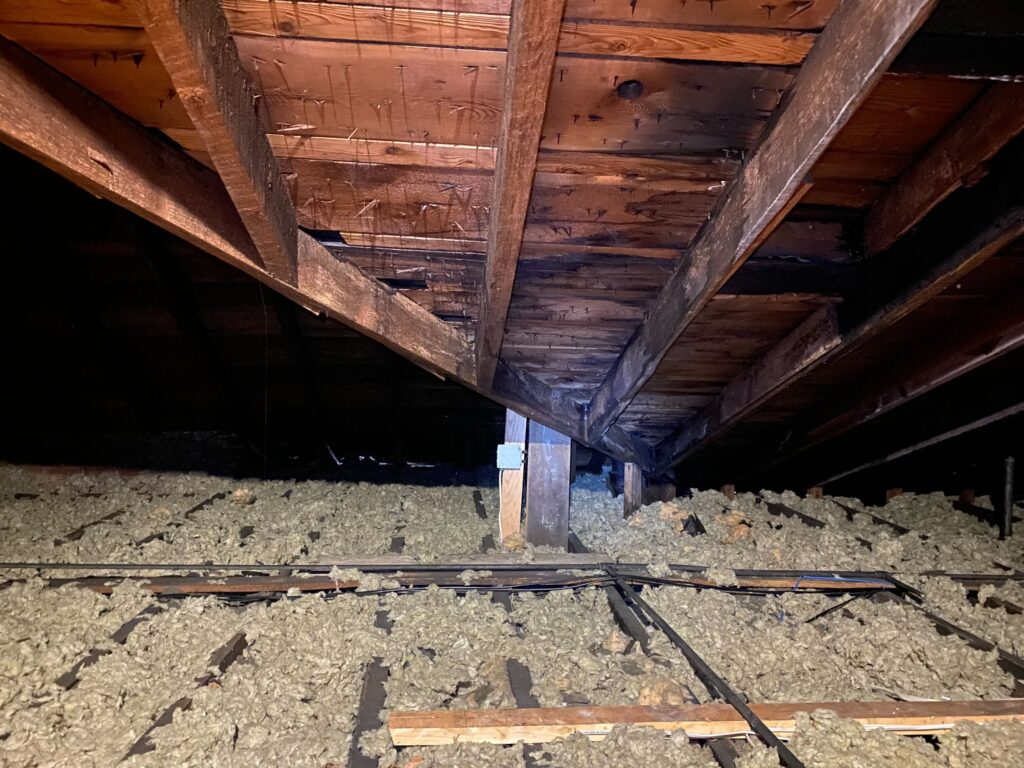
Remote imagery simply cannot offer structural analysis details; this must be done on-site. While drones cannot tell you everything about roof health, they can offer some insight, and an interior verification can check the rest.
In particular, an internal survey should be conducted that checks roof structural integrity (via the attic), the location of support beams, layers of shingles or re-roofs, and how fire setbacks might impact racking installation. You may also want to do a quick roof walk to look for soft spots, or a shingle bend test to evaluate roof material health. If you’re only doing a remote design, you can’t answer any of these questions accurately.
2. Electrical analysis needs on-site surveys
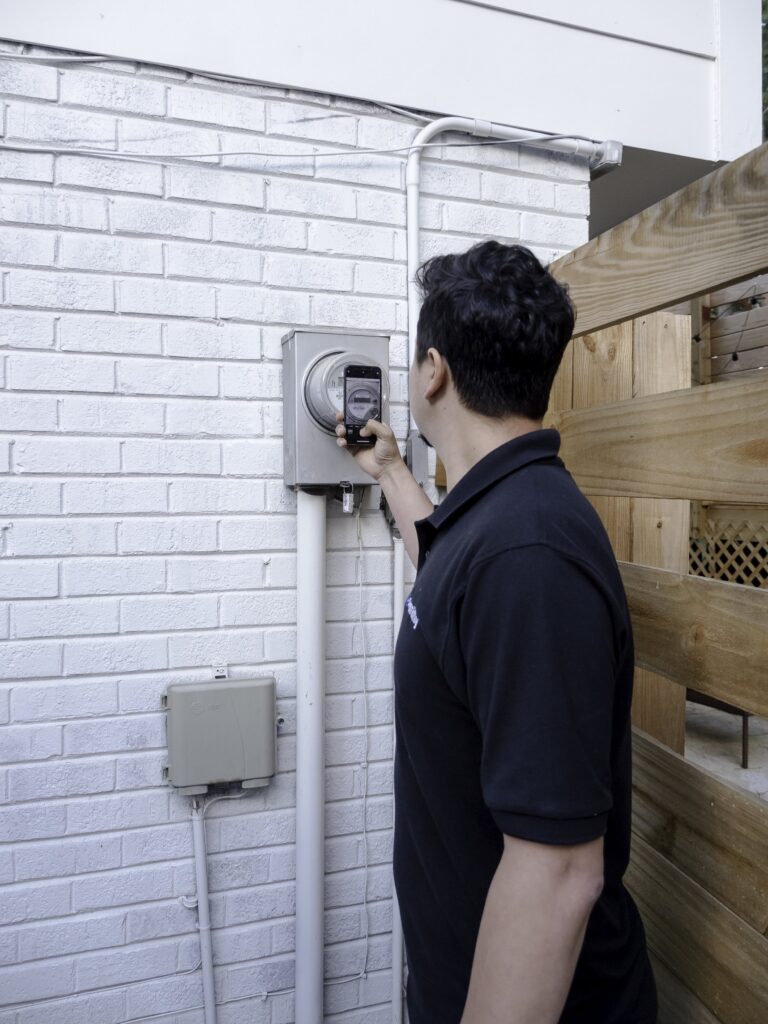
Designers need to know a lot of specifics about existing electrical hardware and where to fit new parts, particularly in older homes, where years of electrical renovations (or electric code changes) can impact future work.
On-site surveys need to collect this information, including meter analysis, main breaker details, wire quality, and what type of hardware might be necessary for the project (e.g. inverters, batteries, disconnects).
They also need holistic context (e.g. the wall where the panel is located) to determine where future hardware is placed.
Unless you’re working on new construction and can rely on builder specs, you need to conduct an on-site survey to collect this information.
3. Perfect roof measurements
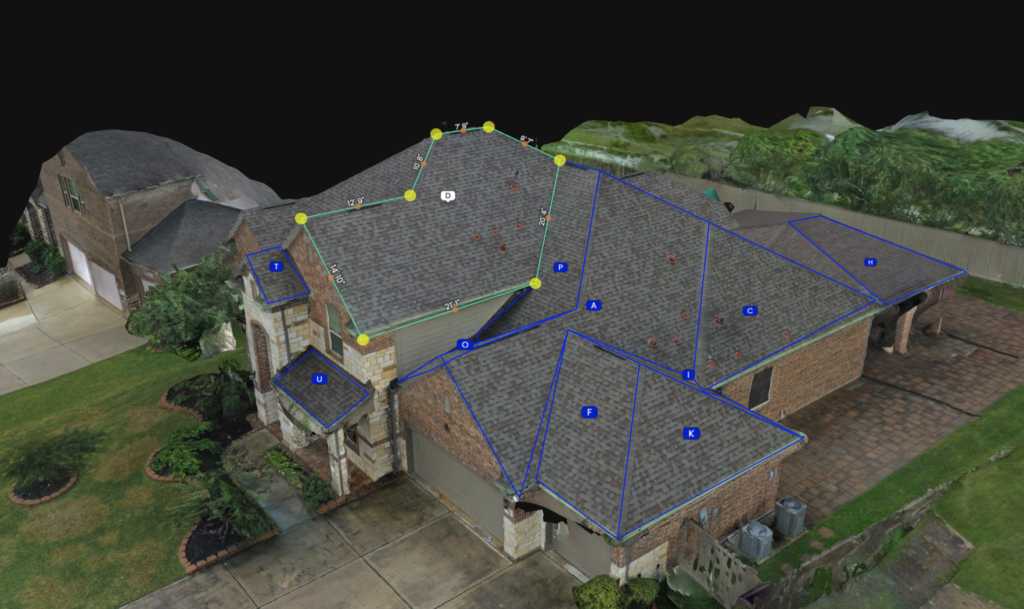
“Perfect” measurements are when data collected from the field is used in a design that always fits on install day.
Satellite and remote imagery match the reality of the site with a tolerance of 6-18 inches. When planning an array, these margins will lead to fitment issues unless there is a lot of open roof space to adjust as you go. This happened to one solar customer who got a preliminary design showing 100% production offset, but poor measurements misinformed the final design, leading to only an 80% offset in the end.
Further, Designers need to know where obstructions are and take into account any setbacks required by AHJs or fire codes. That’s why we recommend using a drone during an on-site survey to measure and 3D-model every roof plane. This allows Designers to plan the best array possible rather than trying to force-fit panels on a single, predetermined roof plane.
The process doesn’t need to have revisions or disappointing customer experiences. Using technology like drones and mobile apps delivers accurate data from the first on-site survey – see countless examples, including Namaste Solar, Dynamic Solar, and others.
4. Verifying shade analysis
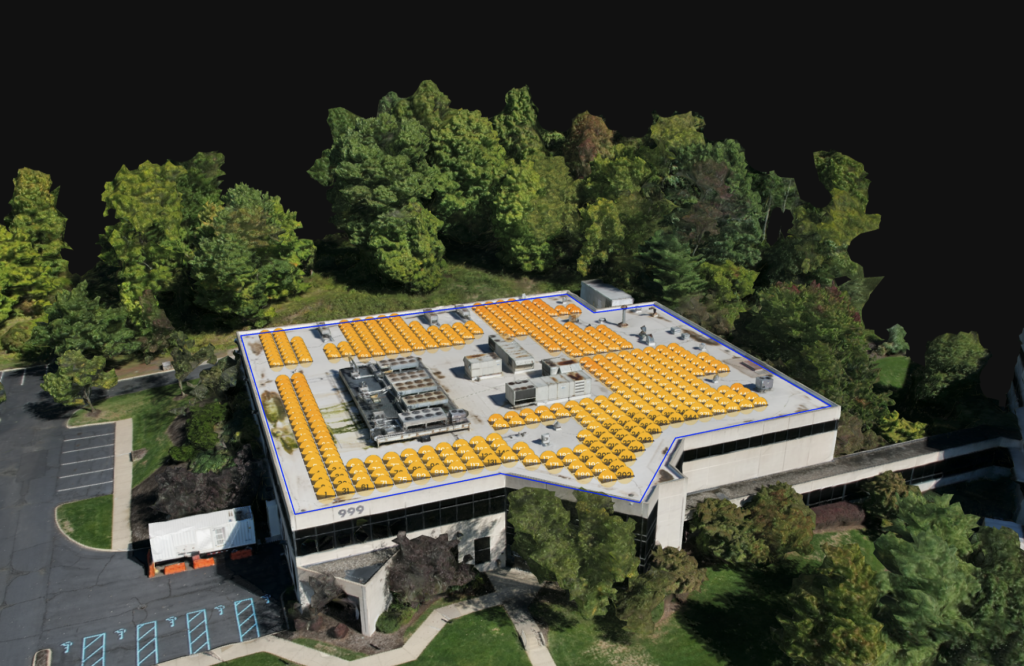
The vast majority (81%) of Surveyors acknowledge that on-site shading is better than remote shading data. And it’s not difficult to see why —remote shading data is often incorrect due to old or incomplete information. Even something like a neighbor planting a new tree six months ago can severely impact shade analysis.
The key to success is converting on-site data into a 3D model using drones and photogrammetry, which enables on-site data to be analyzed remotely. Since shade is one of the pivotal issues limiting maximum solar production, it’s essential to get this analysis as accurate as possible (particularly if you offer production guarantees).
Don’t Prolong a Time-Consuming Solar Design Process
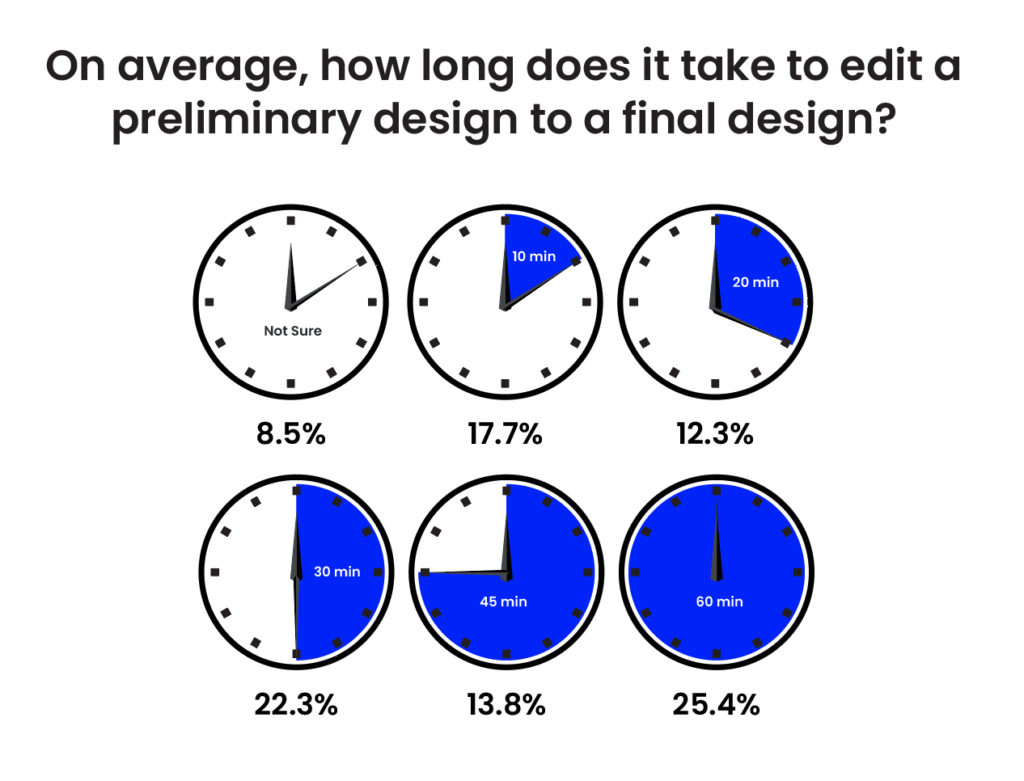
Building a complete plan set — that is, documents Installers can actually use to install and commission the array — is a fairly routinized process today, but still requires a decent amount of Designer time. For example, over one quarter (25.4%) of Designers spend over one hour per project to build a full plan set. And the majority (61.5%) take 30 minutes or more per project.
With the amount of time already going into high-quality final designs, the last thing Contractors want is inaccurate data causing further delays. Unfortunately, this is commonplace with manual surveying methods — 86% of Designers say incorrect manually collected data is the single biggest issue causing problems in design.
In the Design phase, this simply means more time and, in some cases, another truck roll or educated guesses based on similar properties. But this also leads to revisions, with 66.4% experiencing revisions on at least one quarter of their projects or more. And these delays don’t even take into account issues Installers might still have to fix.
Better plan sets, better projects
Remote designs are valuable to start sales conversations and discuss the financial details of going solar. However, in most cases, you need to get on-site data before finalizing engineering documents and filing permits. And the best way to do that is with technology.
Rather than relying on manual surveying methods, which are both time-consuming and dangerous, use drones and mobile apps to safely and quickly collect data in a central repository. From there, Designers can operate accurately and efficiently with genuine data—all leading to higher quality, comprehensive plan sets.